There are several factors to consider before investing in injection machines. Injecting pressure depends on L/D ratio, which is the ratio of the screw's length to its largest diameter. The ratio ranges from twelve to twenty, and a higher L/D ratio results in a gentler shearing action. Injection machines are generally more expensive than extrusion machines, but they are a necessity for manufacturers. Here are a few other important considerations when buying an injection machine.
Injection machines are used to create plastic products. They consist of several parts, including the barrel and hopper. A hopper feeds the material to the barrel. The barrel has a ram injector that forces the material forward. A reciprocating crew pushes the material, which forces the resin into grooves in the screw. The screw back speed and pressure control the mixing speed. The carriage can be moved to sit on the sprue, allowing it to be retracted for purging or dosing.
The market for injection machines in the North American region is expected to grow at a moderate rate over the next few years. The growth is expected to be limited by the presence of a small number of well-established machine manufacturing companies in the region. Another factor that could hamper growth is the shortage of labor in the manufacturing sector. In addition to the emergence of new applications for injection machines, the increasing use of the technology will help in the manufacturing of new products.
Electrical injection machines must meet the safety requirements outlined in this Annex. They must be equipped with safety interfaces and movable guards. They can also feature fixed guards that prevent unintentional contact with hot parts and indicate a high temperature. A movable guard with a safety switch must be used on injection units. The design of these guards should take into account the extreme positions of the nozzle and the risk of plasticized material splattering.
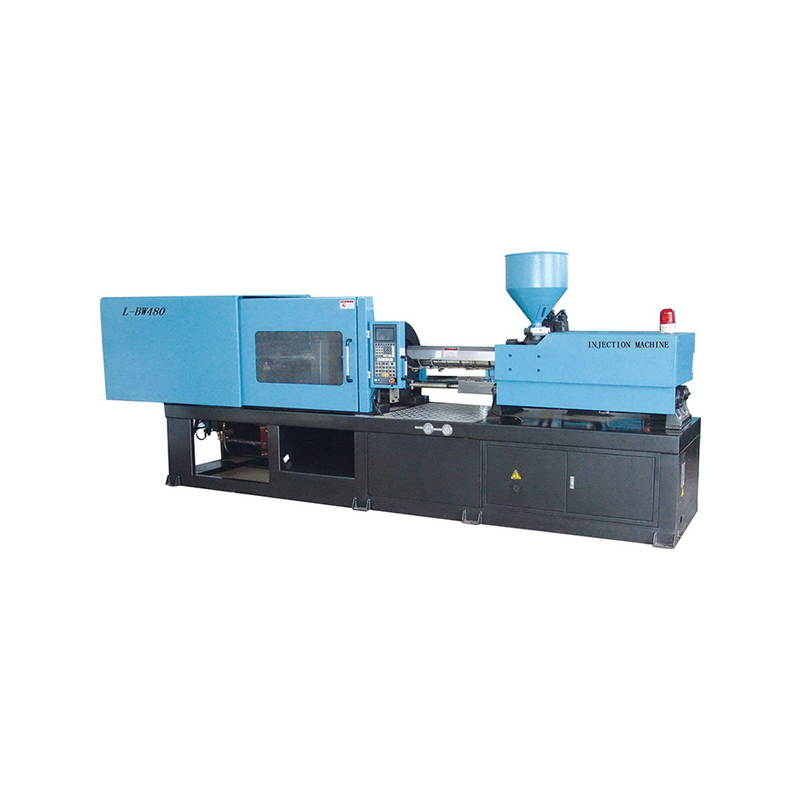
Another important consideration is the viscosity of the plastic. Flow length and pressure depend on viscosity. The higher the viscosity, the longer the cycle time. The longer the cycle time, the less pressure is available. If viscosity is lower than the required viscosity, the sprue gate will have a difficult time filling the mold cavity. Injection pressure and viscosity depend on each other.
A hybrid machine uses an electric motor to drive the axis, but is still hydraulically driven. A servo motor controls the pump and helps reduce energy consumption. A fully-hydraulic injection machine utilizes a servo motor to drive the pump. These machines have variable displacement pumps, while semi-hydraulic ones have a fixed displacement pump. The difference between these two types of machines is the servo system and the accumulator.
Screws vary in shape and size. The two main types of screws have different functions. The metering screw is at the rear section, with a smaller diameter, while the melting zone is in the middle section. A check ring is installed at the tip to prevent resin flow during retraction. The screw can be specialized to handle different materials, depending on the manufacturer. These are some of the more popular types of injection machines. Once you've chosen the right one, you can start molding.