The second is material heat treatment. The material processing technology is the concentrated expression of the gap between China's compression molding technology and foreign technology. The third is the fine processing of the thread surface. The thread determines the various skills of plastic bottle caps. Therefore, this link is the primary link. Mainly by turning, buckle, spark processing, etc.; Fourth, high-precision grinding, grinding is attributed to the last process, which has a key impact on the quality of the bottle cap. The plan of the plastic bottle blowing mold is based on the requirements of the plastic bottle cap structure, and the plastic bottle cap compression molding mold is planned to be installed,
1. Positioning plate 2, upper fixed template 3, upper discharge plate 4, flow channel plate 5, lower fixed template 6, base plate 7, movable template 8, shaft sleeve 9, planetary wheel 10, backing plate 11, guide plate 12, Threaded sleeve 13, lower fixing plate 14, shaft sleeve 15, sun gear 16, shaft sleeve 17, main shaft 18, pulling pin 19, runner pouring gate design The mold designed in this article is primarily filled from the base of the mold, so It can prevent the appearance of air during the molding process of plastic bottle caps, resulting in excellent exhaust performance. However, according to the closure requirements of the bottle cap, in order to improve the strength of the thread and prevent it from appearing bubbles during the injection molding process, it is possible to set the point gate at the bottom base of the plastic part, so as to improve the fluidity of the plastic and improve the quality of the product. quality. The detailed planning structure of the limit organization plan is as follows: during operation, the upper discharge plate (3) is separated from the runner plate (4), and some of the movable molds also move backwards, and the upper fixed mold plate (2) is made under the effect of the pull rod. ) and the upper discharge plate (3) are also separated, take out some of the condensed material in the flow channel, and some of the moving die will move back accordingly, under the effect of the end face limit of the small tie rod, the upper fixed plate 4 (2 ) is separated from the backing plate (10) to complete the corresponding demoulding action. Plastic bottle blowing mold processing technology Based on the analysis of the mold design, in order to reduce workpiece deformation and processing errors during processing, the correct processing technology should be reasonably used on the basis of standard mold design standards, as follows:
In the key parts of the mold, reasonable planning and processing of the core chamfering and cornering should be carried out to ensure that there is enough space for it. It is mainly based on the subsequent processing elements. The processing of plastic bottle caps usually requires rough processing. Finishing after processing will prevent the volume of plastic bottle caps from becoming smaller due to the lack of preliminary allowance during finishing. Sufficient space should be reserved during roughing to ensure that there is enough scale after heat treatment. processing. Scientific calculation of grinding results Grinding is an important part of the processing of plastic bottle caps. It is mainly a method of using abrasives to remove materials, and it is a method of improving the accuracy of plastic bottle caps. Because the allowance for grinding is relatively small, it is The operation of this link needs to be strictly calculated, and the chemical reaction of the touch surface, the touch temperature and the load type should be fully considered. It is often difficult to eliminate the quenching stress during the processing of the plastic bottle cap mold, so the advanced treatment + high temperature tempering plan can be adopted, but the tempering temperature needs to be controlled in the implementation, and the practice has proved that the temperature of 520 degrees Celsius is selected Tempering can improve the strength of the mold;
At the same time, the number of standard temperings is also required to ensure that three temperings are carried out. Dealing with flash problems Flash usually occurs in the parting position of the mold. The main reason for this problem is that the pressure is too large or the injection speed is fast during the injection molding process. Therefore, the countermeasures are mainly from the following aspects manpower:
One is to improve equipment performance. Usually, when selecting the model of the injection molding machine, the additional clamping force calibrated by the machine is usually greater than the tension caused by the axial cross-sectional area of the injection molding part during injection;
The second is to update technical measures. Detail is the time to extend injection molding;
The third is to redesign the mold. High-precision plastic molds are the key elements to ensure the completion of reasonable processing techniques and the quality of plastic parts. Therefore, we must strengthen the research on the design and processing of plastic bottle cap molds, so as to promote the realization of the strategic goal of China's manufacturing power.
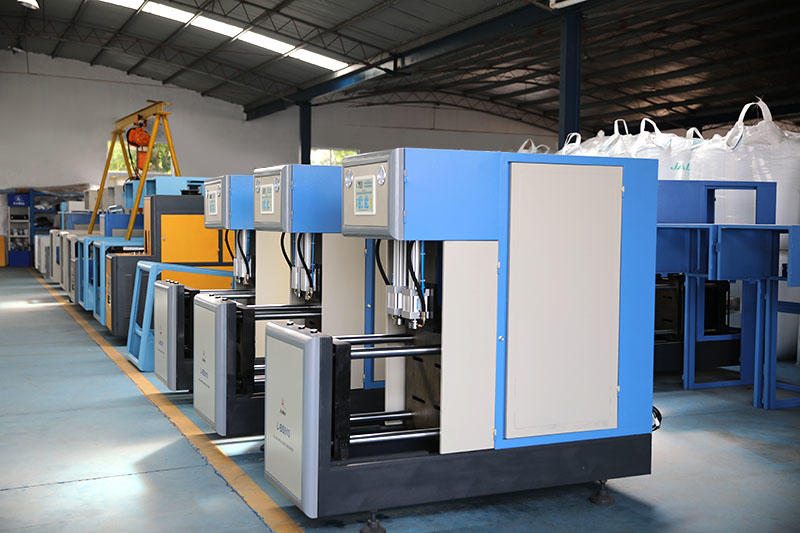