The process of plastic bottle moulding starts with feeding granular plastic into a storage container. It is then passed through a heated section with motorized threads to melt the granules. Once the plastic is melted, it is transferred into the mould where air forces it to take the shape of the container. The mold is then removed from the machine. Plastic bottles are then ready for packaging. The process has several benefits. Unlike traditional bottle moulds, blow moulding machines can be customized and offer low MOQs.
The Blow Molding process involves a process called Compression Blow Molding (BBM). The BBM method enables precise bore and thread tolerance and an increase in thread definition. It is especially useful for bottles with tight neck tolerances. Lastly, it is an ideal choice for a range of different materials. These materials are remarkably versatile. The BBM process is highly versatile, allowing you to create plastic bottles that fit into various shapes and functions.
As a result, BMT provides the software, hardware, and services that allow bottle manufacturers to design their products with better material use. By utilizing the data, bottle designers can make informed decisions about the best material choice for the final product. The new technology has been integrated into the design process for billions of containers. The BMT process is an ideal example of how the new technology can be used in bottle design. The BMT team is collaborating with major companies around the world to make bottle caps with the highest quality.
A plastic bottle mould is a critical component of bottle production. It is the essential part of a bottle. The cap protects the contents of the bottle, which makes it a must-have in everyday life. A bottle cap mould makes it easy to create caps for bottles. To get started, first remove the labels from the bottles and clean them thoroughly. After that, cut them into small pieces and fit them into a metal container. Once this is done, the process is complete!
Embossing is an important feature of hard plastic bottle moulds. The process adds writing or a logo. It also reduces the need for labeling. An embossed bottle cap makes the lid easily noticeable when it is opened. Furthermore, embossing does not increase the cost of production and is a longer lasting solution than labeling. When used properly, it provides the best quality and value for your money.
Injection molding is a common method for making high-volume plastic parts. It can even be used to make parts for surgical devices. The process is efficient and environmentally friendly. However, the cost per unit of plastic bottles and jars is expensive because the mould needs to be made of steel or aluminium, which are highly durable and resistant to wear and tear. The price per unit drops dramatically when production volume increases, but tooling can take up to 16 weeks, and the production time is as short as four weeks.
It can produce bottles with up to 7 layers of materials. Virgin plastic resin encases a barrier layer (PCR), and the last two layers are bound together by adhesive. While each manufacturer has its own capabilities, common capabilities include in-mould labeling, window stripe on bottles, and multiple necks. It is important to consider all these factors when selecting a plastic bottle mould to suit your needs.
Injection moulding requires a higher temperature for the plastic material to reach the pouring point. The benefit is a high-volume process that has minimal energy use. The downside of injection moulding is that you cannot easily replace the mould cavity. In addition, the cycle time is much shorter. It also results in higher production capacity. This process also offers less pollution. It is a good choice for producing plastic bottle caps. For more information about plastic bottle moulds and its benefits, contact us today.
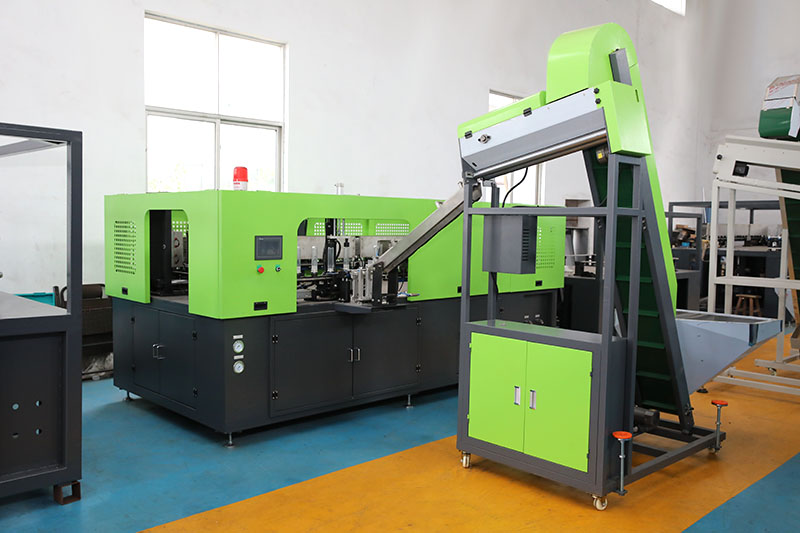