Though the process had great potential, many types of plastic were not available to manufacturers. However, World War II increased the need for synthetic plastics, and engineers responded by developing new plastic varieties. The plastic bottle quickly became a popular item. It is not surprising that the blow molding process has become one of the most popular types of plastic containers today.
The blow molding process begins with the creation of a preform, a hollow plastic tube. This preform is inserted into the mold via a metal ram. The ram forces the parison through the mold cavity, which must match the product's height. The plastic part is then clamped inside the mold. Depending on the cavity, the final shape of the plastic product is determined. Air pressure is applied to the inside of the preform by a blow pin. This air pressure causes the parison to expand and take the shape of the mold cavity.
Another type of blow molding involves the use of a stretch blow mold. In this process, a molded preform is heated above its glass transition temperature and then blown with compressed air. The stretching action creates a strain-hardened material, which resists deforming under pressure. In addition, the molecular alignment gives the parts better gloss and burst pressure. This process is commonly used to produce bottles made of polyethylene terephthalate.
The injection blow molding machine uses an extruder barrel and a screw assembly to melt the polymer. The molten polymer flows through the hot runner manifold and into a heated cavity. The cavity mold then clamps around a core rod to form the internal shape of the preform. The finished part is then rotated back to its final station for ejection. There are several types of blow molding machines available on the market.
The first step in the blow molding process involves feeding the plastic resin into the extruder hopper. This process is done through the use of vacuum pumps to draw the pellets from big bags into raw material silos. Then, a rotary feeder at the bottom of the silo controls the rate of feeding into the plastifier. A second method is vacuum conveying. Both methods are effective and safe. However, a single-stage process is not suitable for preform inspection.
The global blow molding machine market is segmented according to type, raw material, application, and region. Types include extrusion, injection, and stretch blow molding. Applications include plastic cans, wide mouth jars, and water bottles. The report covers the key companies, current market trends, and company profiles.
Screws are also important components of a blow molding machine. They are designed to deliver high-throughput while simultaneously ensuring the consistent flow of the material. The blow molding screw, unlike most others, is typically made specifically for a particular material and application. This can be problematic if you're working with a multi-layer blow molding screw head. Therefore, it is crucial to choose a machine with a high-quality screw.
Injection-type machines usually use an archimedean screw to push the plastic forward. In continuous blow molding, the rod presses the parison out to the next station for cooling, inflation, and stripping. It is also characterized by high precision and high speed. There are many types of plastic products made with a blow molding machine.
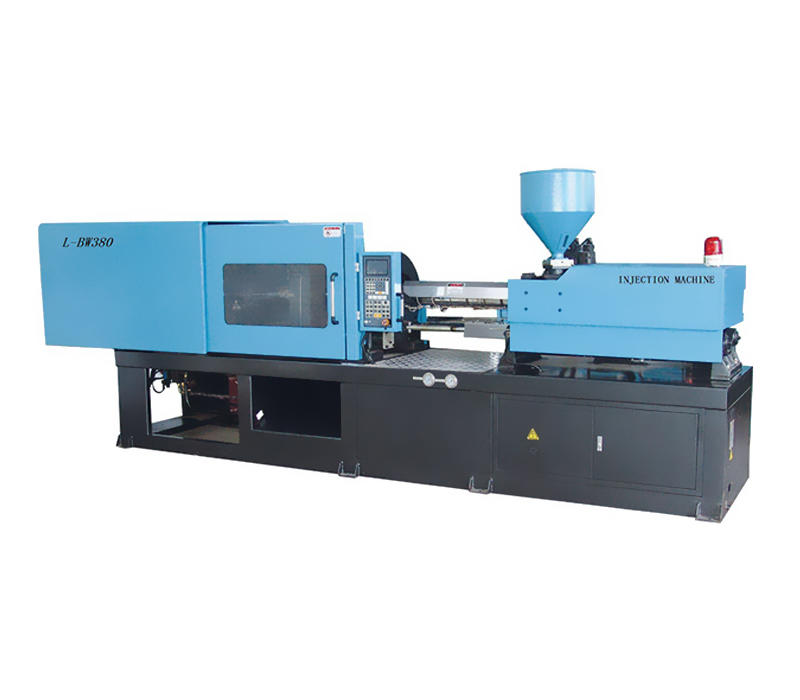