There are various types of Injection machines. Some of these machines are used to make a variety of products, such as toys, medical supplies, and even cosmetics. In some cases, these machines are also used to recycle plastic. To recycle plastic, the correct temperature is necessary. Plastic that melts easily in the Injection machine can be HDPE or PP. Before starting the machine, the material must be placed into the barrel. Wait for five to ten minutes for it to melt. Then, it must be cooled down with water. Once the process is over, the finished product is produced.
Typically, post processing is required following the injection molding cycle. The excess material that has solidified in the mold must be removed from the part using cutters. Plastic trimmings can be recycled by a plastic grinder, also known as a granulator. Plastic grinders grind waste material to pellets called regrind. To make these pellets, the scrap material must be mixed with the raw material in the right regrind ratio. After the process is complete, the parts are ready for packaging.
A plastic injection machine has many parts. It consists of a hopper, feed throat, screw section, and ejection nozzle. The injection unit controls the melt temperature, injection speed, and shot volume. Once the molten plastic has reached the correct temperature, the machine opens the mold and pushes the solidified part out of the open cavity. These machines are widely used for producing high-quality plastic products. Its advantages over other machines are numerous.
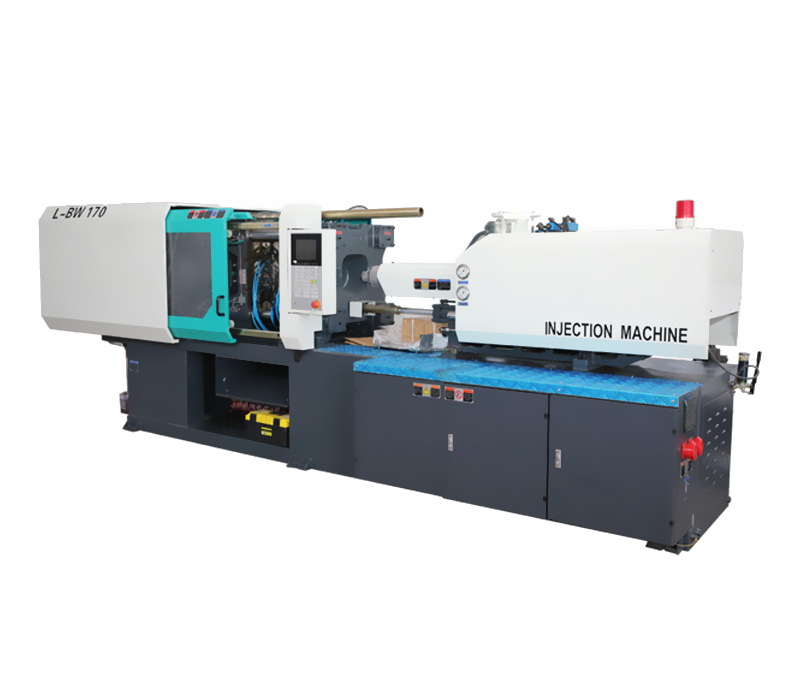
The process specifications of the Injection machines are approximate. Their actual capabilities depend on the machine, material, and requirements. It is difficult to accurately calculate the injection time as the amount of molten plastic changes continuously. However, the injection power and shot volume can be used to estimate the time required for each process. A good quality machine is one that can meet all your specifications. When you're looking for a new injection machine, make sure to check the specifications before buying.
A general purpose screw is used with virtually all injection molding machines. This screw is designed to meet the requirements of most thermoplastics. Some injection molding machines even offer additional screw options, such as a vented screw with an exhaust port and decompression zone. The more tonnage the machine has, the larger it will be. But even if it's not enough, it will still be more expensive than a machine that uses a different screw for every material.
Auxiliaries are used for several different purposes. Auxiliaries pick up finished parts, sprues, and scrap material from the molding equipment. Auxiliaries also use granulation equipment to reduce scrap material into useful materials. Auxiliaries eliminate a range of inconsistencies in material, temperature, and process, and contribute to high-quality production. You will be surprised at the many advantages of an injection machine.