Basically, blow molding is intended for the manufacture of hollow plastic products, such as bottles and other containers. However, the process is also used to produce toys, automotive parts, accessories, and many engineering components. The principles used in blow molding are essentially similar to those used in the production of glass bottles. Although there is considerable variation in the processes that can be used for blow molding, the basic steps are the same: (1) melting the plastic; (2) forming the molten plastic into a form blank (a tube of molten plastic); (3) sealing the end of the form blank, except for an area through which blowing air can pass; (4) inflating the form blank to assume the mold in which it is shape; (5) cooling the blow molded part; (6) ejecting the blow molded part; and (7) trimming the flash, if necessary. The two basic processes of blow molding are extrusion blow molding and injection blow molding. These processes differ in the way the blanks are manufactured. The extrusion process uses unsupported blanks, while the injection process uses blanks supported on a metal core. By far, the extrusion blow molding process accounts for the largest percentage of blow molded products produced today. However, injection processes are gaining acceptance. Although any thermoplastic can be blow molded, polyethylene products made by this technique dominate. Extruded polyethylene bottles account for a large percentage of all blow molded products. In the molding process, air pressure is used to inflate the soft plastic into the mold cavity. It is used to make one-piece hollow plastic products with thin walls, such as bottles.
Done in two steps.
Construct a starting tube.
Inflate the tube to the desired final shape.
The type blank can be molded using either extrusion or injection molding.
Extrusion Blow Molding
Extrusion is the most basic when it comes to blow molding. Using an extruder and a water-cooled die, the type blank or thermoplastic tube is clamped in a piece of plastic. Just like blowing up a balloon, once the die is closed, air is pumped into the mold. The material is fed through the feed hopper into the feed transfer screw in extrusion blow molding. To make the part, the extrusion blow molding machine uses a hollow tube as the tool. We call this tube the type blank. To blast the type blank, the hollow die is closed around it. Air pressure is used to form the blanks inside the die as another blanks is extruded from the machine. Thus, the production process can be completed faster
Working principle of extrusion blow molding machine
Extrusion blow molding dies
In order to create the form blanks, a specially constructed blow molding die is used to extrude the material into a hollow tube. Compared to injection blow molding, extrusion allows for larger parts to be made. It is also cheaper because there is no internal tension in the part. On the other hand, extrusion blow molding generates more waste and provides less control over the accuracy of the basic dimensions. Depending on the specific application, extrusion blow molding can be run as a continuous or semi-continuous process.
The material is fed through a feed hopper into a feed transfer screw in extrusion blow molding. A specific blow molding die is used to direct the material flow into a hollow tube called a form blank. Gravity causes the blank to drop until it reaches a predetermined length, at which point the die closes around it and seals the bottom edge (thus providing a unique end seal). The blank is cut, the blow pin moves to the top of the tool, and a cutting knife is used to blow the blank against the wall of the tool cavity. Once the tool has solidified, it is ejected from the tool and the process is restarted with an extruded new type of blank. Figure 2 depicts a diagrammatic representation of this system. [2]
Extrusion blow molding process
Extrusion blow molding process
Extrusion blow molding applications are divided into six categories based on their function.
1. Petrochemicals and Chemicals
Most petrochemical and lubricant containers are manufactured by blow molding methods, usually using HDPE or LDPE as the material. Examples include plastic fuel tanks, oil bottles, petrochemical tanks, oil drums, lubricating oils, gum grease, etc. Sometimes multilayer technology is used on these containers as it improves gas barrier and further extends storage life. In addition, it can be more environmentally friendly and cost saving due to the use of recycled materials. Jamin is experienced in multi-layer technology and can advise you on how to archive your target.
Blow molding example: plastic fuel tank blow molding example: motor oil bottle
2、Food packaging
Food packaging is used to fill from thin liquids to thick liquids. Examples of thin liquids are soy sauce, vinegar, cocktail sauce, cooking oil, fruit juice, etc. Milk bottles, yogurt, lactic acid drinks, butter, jam, sauce, ketchup, honey, mustard, salad dressing, mayonnaise, ketchup, vinaigrette, chili sauce, etc. are examples of thick liquids. Oxygen-sensitive mayonnaise, ketchup or sauces often require multiple layers of packaging to preserve the product. Some products also require an acid-resistant layer or UV barrier to ensure food safety and extend shelf life.
Blow molding example: milk bottle blow molding example: ice popsicle
3. Cleaning products (household)
For example, liquid cleaner, floor cleaner, floor polish, glass cleaner, kitchen spray, detergent, bleach, bath cleaner, bathroom spray, car polish, degreaser, etc.
4. Medical supplies (pharmaceutical)
Pharmaceutical or biopharmaceutical products are packaged using a variety of plastics. HDPE cans are commonly used for pills, capsules, vitamin supplements, daily supplements, nutraceuticals, powder shakes, nutritional supplements, protein shakes, collagen powder, etc. LDPE is commonly used for liquid products such as syrups, cough suppressants, lordine, liquid vitamins, liquid gastric relievers, nasal washes, nasal sprays, eye drops, contact solutions oral liquids, enemas, etc. This is an example of a protein shake can.
PVC is used for oxygen masks and PP is usually used as dropper bottles.
Blow molding example: Protein shake jar Blow molding example: Oxygen mask
5. Personal care
Personal care products widely use PET, PP, PE as packaging materials. For example, shampoo, conditioner, hair dye, lotion, cream, cleanser, moisturizer, toner, skin cream, perfume, sunscreen, sunscreen lotion, sunscreen oil, sunscreen, mascara, essential oil, makeup remover, face wash, hair styling gel, hand cream, massage oil, mask, mud mask, liquid bubble bath, intimate oil, nail polish remover, shower gel, etc.
Blow molding example: personal care bottle blow molding example: shampoo bottle
6. Others
Blow molding machine can make various shapes of toys, wind boxes, knife cases, roller balls, tool boxes, teapots, car parts, tables, barricades, dumbbells, plastic sports equipment, tree ornaments, etc.
Blow molding example: barricade blow molding example: blade shell
Injection blow molding (one stage) process
By injecting a plastic bottle blank and transferring it to a blow molding station via a rod, the bottle blank is molded and then shaped under air pressure according to the design of the negative blow mold, a process known as injection blow molding. A typical injection molding machine can perform a single-stage injection blow molding process without bottle blank storage and reheating to produce small series of custom hollow parts. After a short cooling period, the preforms are blow molded.
For this type of application, polypropylene (random copolymers) is preferred. Temperature gradients, molecular orientation, high stretch rates and high cooling rates are all part of this single-stage process. It is quite simple. Smaller processing windows are created by constraints. The preforms must be heated sufficiently for blow molding to allow the process to occur between the melting and crystallization temperatures. Single-stage injection blow molding technology can now be used on common injection molding machines.
Blow molding and injection molding are handled by a single tool in the injection mold. Therefore, it is scaled to match that of a typical injection molding machine. Putting these two steps in the same mold results in a more restrictive process than the typical steps. Temperature gradients, molecular orientation, high stretch rates and high cooling rates are introduced throughout the process. This results in a very narrow window of opportunity for processing. In order for the process to occur between the melting and crystallization points, the preform must be kept sufficiently molten for blow molding.
Injection Blow Molding Process
A single-step infusion of small pharmaceutical and disposable bottles is produced on a large scale using an IBM (blow molding machine). Injection molding, blow molding and ejection are the three stages of the injection blow molding process. In order to melt the polymer, a combination of extruder barrel and screw assembly must be used. Hot runners are used to inject the polymer into the heated cavities and core pins of the mold. The external shape of the preform is made from a cavity mold that is clamped around the mandrel to form the internal shape. To create the body, a thick polymer tube is glued to the neck of the bottle/jar. The bottle preform is completed using a mandrel that is rotated in the bottle preform mold and then clamped into a hollow, cooled blow mold.
A small hole in the mandrel allows pressurized air to enter, expanding the preform into its final form. The blow mold is opened and the mandrel is allowed to cool for a period of time before rotating to the ejector position. As an alternative, the finished product can be leak tested prior to shipment. Preforms and blow molds typically have 3 to 16 cavities, depending on part size and production. Three mandrels can be used to inject, blow mold and extrude preforms simultaneously.
One-Step Injection Blow Molding Machine
Stretch Blow Molding Applications
Soda, juice, and water bottles.
Shampoo and cleaning containers.
Cosmetic bottles.
Medical packaging.
Drums made of plastic.
Bathtubs.
And much more.
Stretch blow molding machines can produce more than 3,000 bottles per hour, producing beverages, food packaging containers and cleaning products.
Most pharmaceutical and cosmetic bottles have necks and other dimensions that must be precisely measured. Another ideal match for this business is a single-stage injection blow molding machine. Plastic blow molded bottles ranging in size from 5 ml to 2 liters are available in a variety of designs.
Detergent and laundry bottles as well as liquid soap and lotion bottles are the most common injection blow molded parts used in hotels and in our daily lives.
Injection stretch blow molding (two-stage)
Injection stretch blow molding (ISBM) uses injection molding to mold plastic into "preforms". During the production of these blanks, the neck and threads of the bottle (called finishes) are incorporated. To manufacture these preforms, the blow molding method is used.
The use of stretch blow molding (a type of blow molding) allows for the production of high quality bottles with extremely high clarity.
The technology used in two-stage injection stretch blow molding machines involves two machines. These are the injection molding system and the stretch blow molding machine.
Here, the plastic is molded into completely cooled preforms in the first machine and then transported to the second machine.
The blanks, which usually have necks and threads, can be sold to third parties even before they are blown using the second machine.
When the latter are received, they are finished, reheated using infrared radiation, and conditioned before being molded.
The need to cool the preforms before reheating and stretching also gives the process its name, the "cooled preform method".
In the two-stage injection blow molding process, the preforms are completely cooled and then transferred to another machine to be blown into their final shape. The preforms must be reheated and then blown. By using two stages, shipping costs can be reduced by transporting the bottle blanks instead of transporting the empty bottles to the bottling plant. The bottles are then blown at the bottling plant prior to filling.
Processes involved in the two-stage method
Dehumidification and drying of the PET material.
Injection of the molten material into the preform die by means of an injection machine.
Cooling of the molten PET preforms to room temperature.
Processing of the preforms by means of a finishing machine.
Transferring the bottle preforms to a reheating stretch blow molding machine.
Blowing high pressure air into the bottle using a metal blow molding mold.
Water, juices, carbonated beverages and various other liquids, such as liquid soaps and detergents, are among the many items typically packaged in plastic bottles using stretch blow molding. After learning the advantages and disadvantages of single-stage and two-stage blow molding machines, the choice will depend on your priorities.
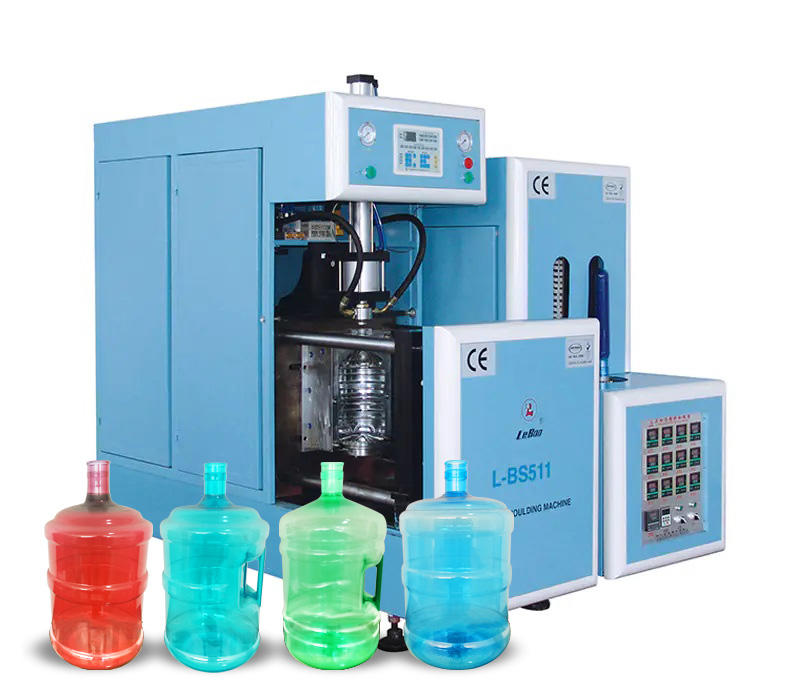